DE-Guiding Issue of my Vixen GP-D2
In Dec 2013 I replaced my Vixen GP-D by a GP-D2. The goal was to gain more stability under full load. At this time full load for my GP-2 was a 90mm triplet refractor with an Atik 383 and filterwheel, guider and a DSLR with tele lens on a DIY tangent assembly. The GP-D2 did well with that load, but the guiding bahaviour went worse, even worse than with my GP-2. Under some conditions everything run well. Only one night later, presumably under equal conditions the guiding was not usable at all. Sometimes I even observed an inverse reaction of the mount on the contol pulse from the guider. Finally I updated this set-up with new worm bearing.
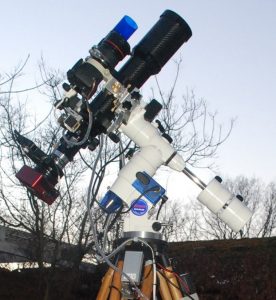
Task of the worm bearing modification
I want to work with reliable equipment. In central europe clear nights are rare. I have neither time nor desire for such a gambling game. Hence I tried to fix that issue. Finde here some details about worm gears.
Root cause for that behaviour is the design and quality of the worm bearings in the GPs. They are extremly simple slide bearings. Basically slide bearings can bring a very good quality. In the GP case the axis bearing is just a bore inside the cast aluminium case. In this bore the brass shaft of the worm is inserted.
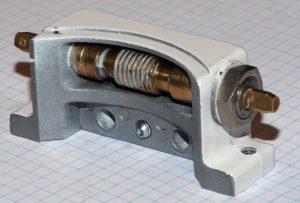
The picture shows the baddie. With this worm bearing only the radial backlash can be adjusted at the side by means of the hex nut and a threaded insert. The worm drives a gear with diameter 74 mm. The GP-2 one is out of aluminium, the GP-D2 one is out of brass. In both cases the gear has 144 teeth. For siderial speed the worm turns with 1 rotation per 10 minutes. I measured the diameters of the DE-worm shafts of my Vixens (one GP-2 and one GP-D2): 6.10mm and 6.04 mm, wherby the bore diameter is always in the range of 6.15mm.
Worm bearing clearance causes DE-Backlash
It is documented sometimes that the SkyScan motors can’t move the GP and stall. This is especially the case at lower temperatures. I assue that the owner (I did so at least) clamped the axial backlash very tight, which at the same time conceals the radial backlash without really removing it. This gives a better feeling, because the force needed to move threw the radial backlash increases. At low temperature the greases viscositiy increases and also the fit between brass an aluminium gets tighter because of different thermal expansion of the materials (αAlu=23*10-6K-1, αMs=15*10-6K-1 ). This increses the torque neede for movement, which at a certain level canot be deliverd by the motor anymore.
In practice, therefore, the fits of the worm shafts can be critical! If you’re s lucky owner of a specimen with correct fits, the radial play is so small that it has no effect when the axial clearance is optimally adjusted. If you are unlucky, the radial play is so large that it can come to a contrary reaction of the mount on the control pulse of the guider. The root cause is the radial mobility of the worm shaft.
Overview of the worm bearing parts
This gallery shows views of the new worm bearing compared with the old parts.
The assembled with its new worm bearing
Here are some views of the mount with the new worm bearing. Find here the some information about the utilization of this mount since 2016.